Moldeo de piezas de plástico ABS
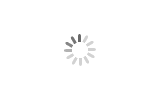
- KCN
- Xiamen, Fujian, China
- 30 dias
- 50000 sistemas por mes
1.Tenemos 15 años de experiencia en la fabricación de moldes y servicios de moldeo por inyección. Podemos personalizar productos según dibujos, abrir moldes y procesarlos como agentes. Los materiales de las piezas personalizadas incluyen ABS, PE, PP, EEE, EVA, PVC, etc.
2.La empresa está ubicada en Xiamen, Fujian, China, con transporte portuario y aéreo conveniente, tiempo de transporte corto y puede recibir pedidos urgentes.
ABS Plastic Injection Molding
Product Name | ABS Plastic Parts | Material | ABS |
Color | Customize | Standard | ISO9001:2015 |
ription | ODM plastic injection molding | Size: | According to your 2D, 3D Drawing |
Package: | Standard exported Wooden box packed, Fumigation process(upon required) | Mold Building Lead Time: | T1, 4-5 weeks, Part measurement report (upon required). |
Mould Life: | 5,000 to 1,000,000 Shots. (According to your working environment.) | Testing Machine | Digital Height Gauge, caliper, Coordinate measuring machine, projection machine, roughness tester, hardness tester and so on |
Drawing Format | .jpg/.pdf/.dxf/.dwg/.igs./.stp/x_t. etc | Surface Finish: | Texture(MT standard), High gloss polishing |
Export Country: | Europe, America, Australian, UK, Canada, France, Germany, Italy...etc.: | Experience: | 15 years experience in plastic injection mold making and plastic prouducts service. |
ABS Parts Injection Molding Process
ABS resin (acrylonitrile-styrene-butadiene copolymer, ABS is the abbreviation of Acrylonitrile Butadiene Styrene) is a thermoplastic polymer material with high strength, good toughness, and easy to process and form.
1: Moisture-proof, corrosion-resistant, non-deformable, insulating, and can also achieve V0 level flame retardancy after material modification, so it is often used in the manufacture of plastic shells for electrical instruments, etc.
2: Because of its high strength, non-deformation, resistance to certain impact and rebound, it is made of this material for children's toys, household necessities, etc.
3: It can be evenly mixed with PC to form PC/ABS alloy material, which improves more strength and toughness on the original basis. Car bumpers are produced from this alloy material.
4: ABS material is also very environmentally friendly. Because it uses environmentally friendly chemicals, it has no toxicity and no smell. It can also be electrically insulated and is a very safe material.
5: ABS material is prone to deformation in an environment where the temperature is too high. Its deformation temperature is 85-105°C, but it has good performance in a low-temperature environment of -40°C.
The injection molding process of ABS plastic mainly includes several steps: raw material preparation, injection molding, post-processing, inspection and testing, packaging and storage.
1. Raw material preparation
Select high-quality ABS plastic particles, weigh and mix them according to production requirements to achieve the ideal formula ratio. Auxiliary materials such as reinforcing agents, flame retardants, colorants, etc. may need to be added.
2. Injection molding
Put the mixed ABS plastic particles into the hopper of the injection molding machine and melt the plastic particles by heating and rotating the screw. The molten ABS plastic is injected into the mold cavity through the nozzle and cooled and solidified in the mold. The function of the holding stage is to continuously apply pressure, compact the melt, increase the density of the plastic, and compensate for the shrinkage behavior of the plastic. 3. Post-processing
After the product is formed, it may be necessary to cut, trim, grind and polish to remove burrs, bumps and other defects. According to the needs of the product, the molded parts are assembled and assembled, and auxiliary materials such as screws and glue may be required
4. Inspection and testing
The molded parts are inspected and measured for appearance to ensure that the product quality meets the requirements. This includes dimensional inspection, functional testing, etc. to ensure that the product meets the design and use requirements1.
5. Packaging and storage
The finished products are packaged, marked with product information and storage conditions, and stored or transported to a designated location
Through this series of steps, ABS plastic can be processed into parts and products of various shapes.
Other injection molding products:
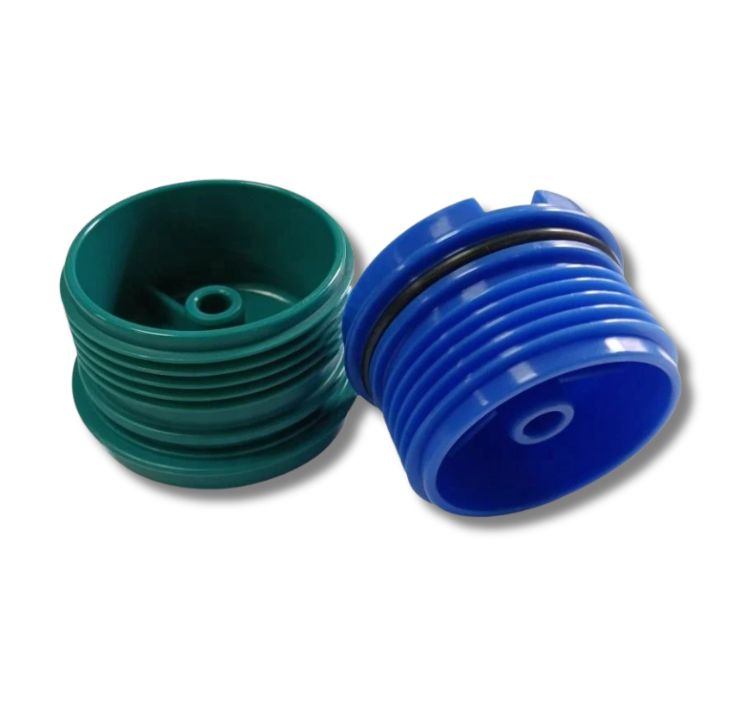
Screw Cap
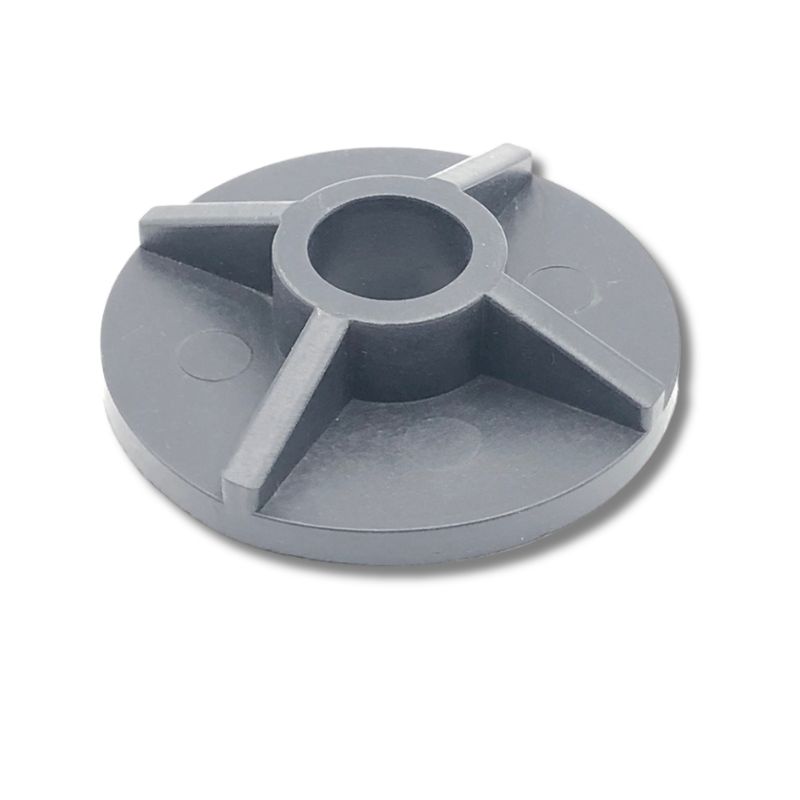
PC Parts
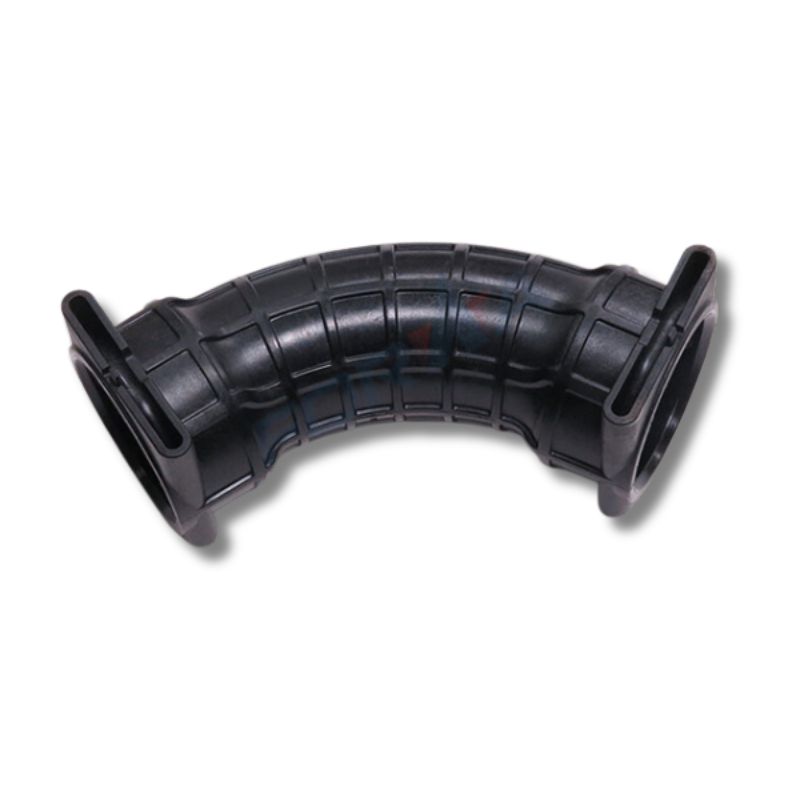
Auto Parts
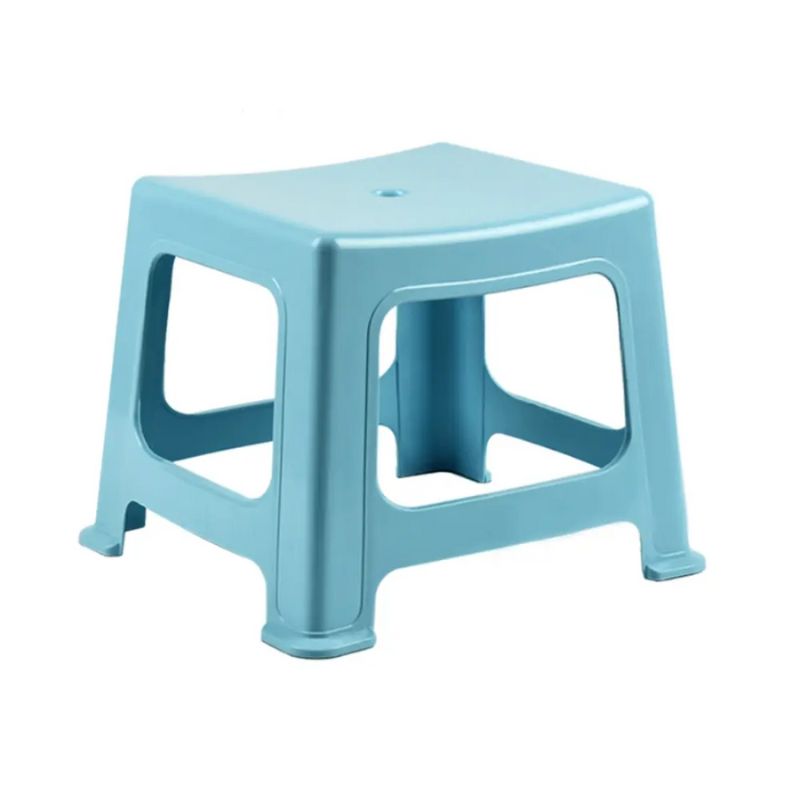
Plastic Chair
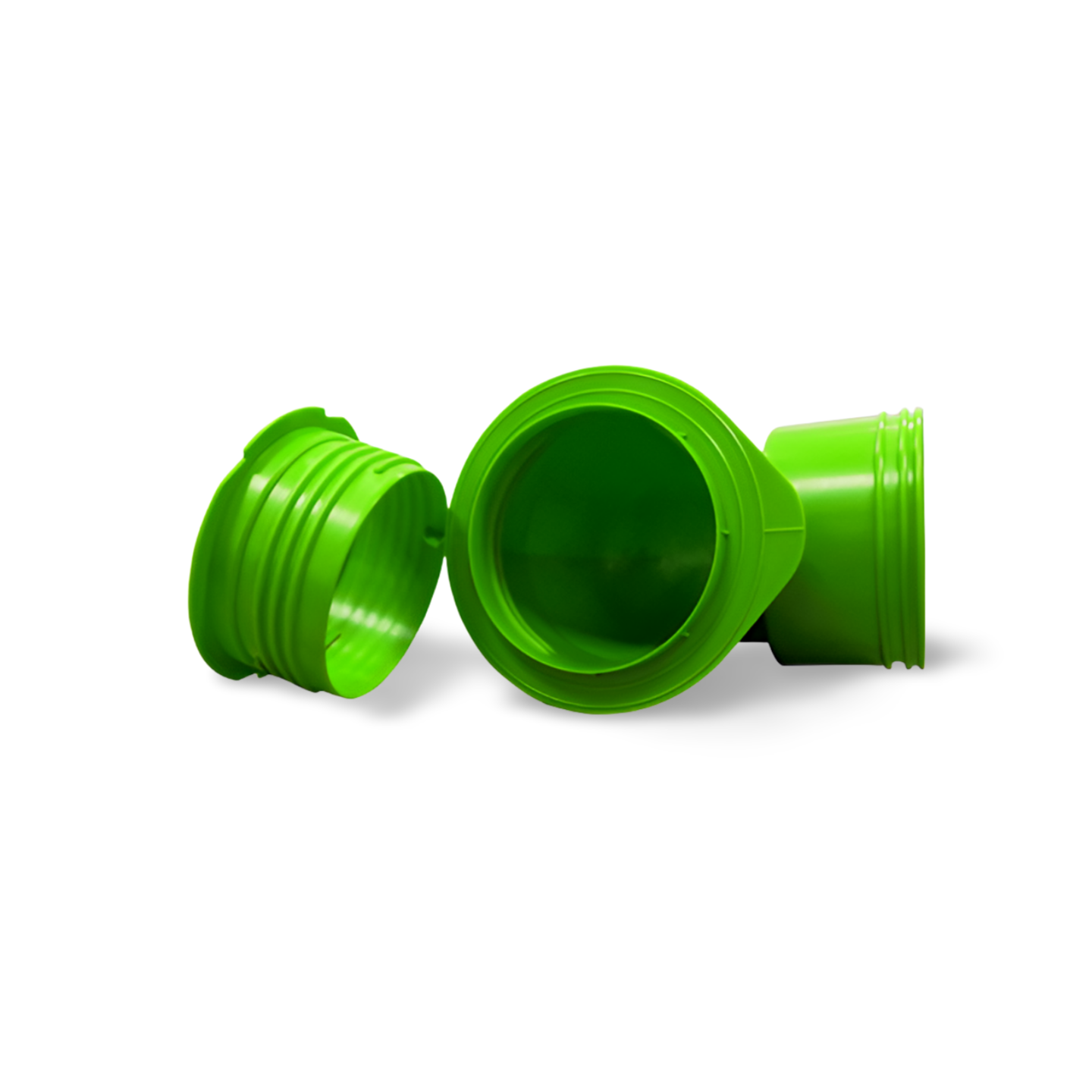
Plastic Elbow
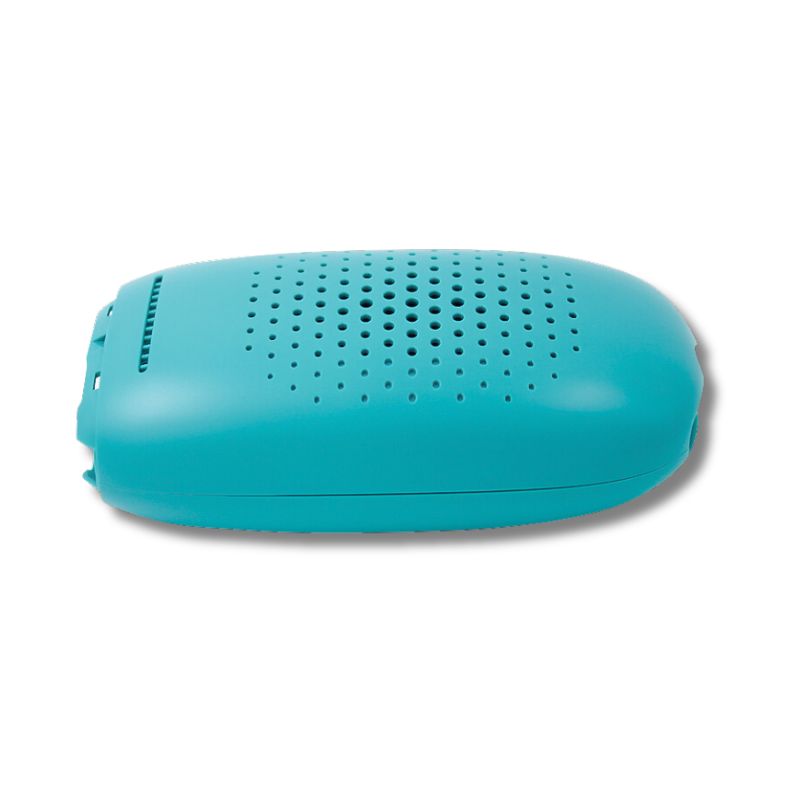
Beauty Instrument
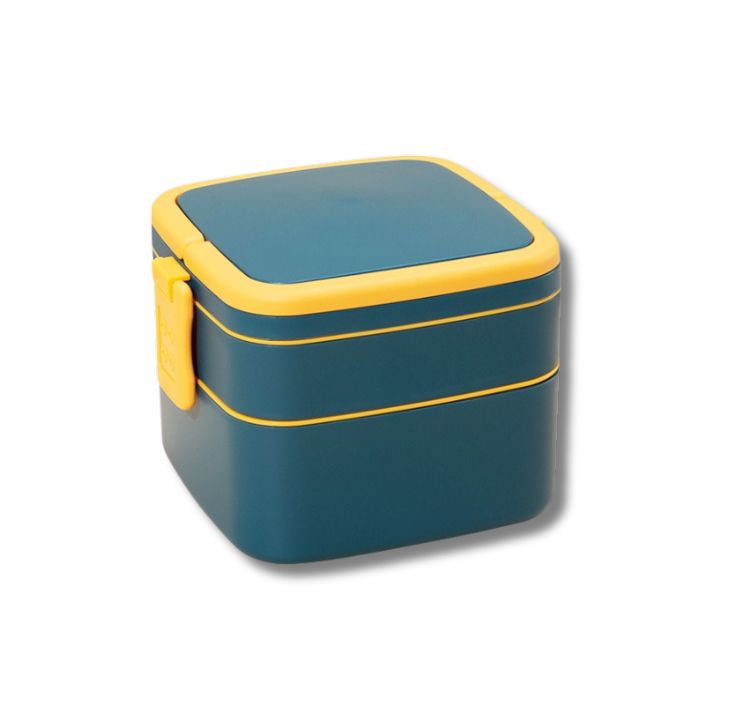
Household lunch box
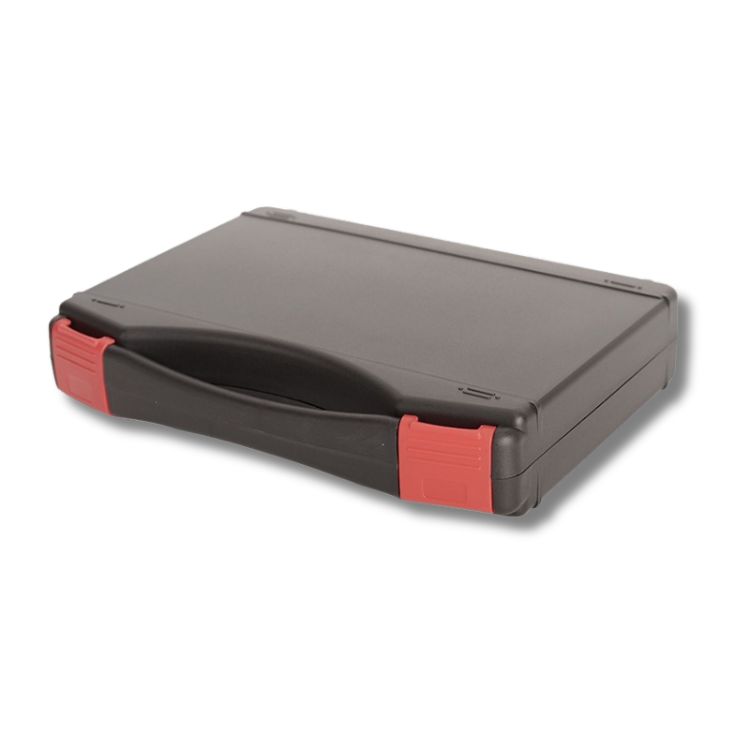
Industrial Parts Box
vanguardia